Introduction
In the manufacturing sector, time is everything. Costs can soar when critical machinery breaks down due to a missing spare part. Therefore, efficient spare parts inventory management is essential not only to reduce downtime but also to sustain smooth production. Today, manufacturing businesses face the challenge of keeping track of thousands of parts across facilities, managing them to balance availability with cost effectiveness.
Increasingly, companies are turning to robust ERP solutions like Odoo to meet these needs. Known for its flexibility, Odoo helps streamline complex processes in inventory management. Here’s how Odoo, primarily when implemented by an experienced Odoo development consultancy, can empower manufacturers to manage their spare parts Inventory precisely, from real time tracking and automated reordering to intelligent stock level optimization and downtime reduction.
Expert Odoo Development Company for Seasonal Demand
Tailored solutions for your business needs.
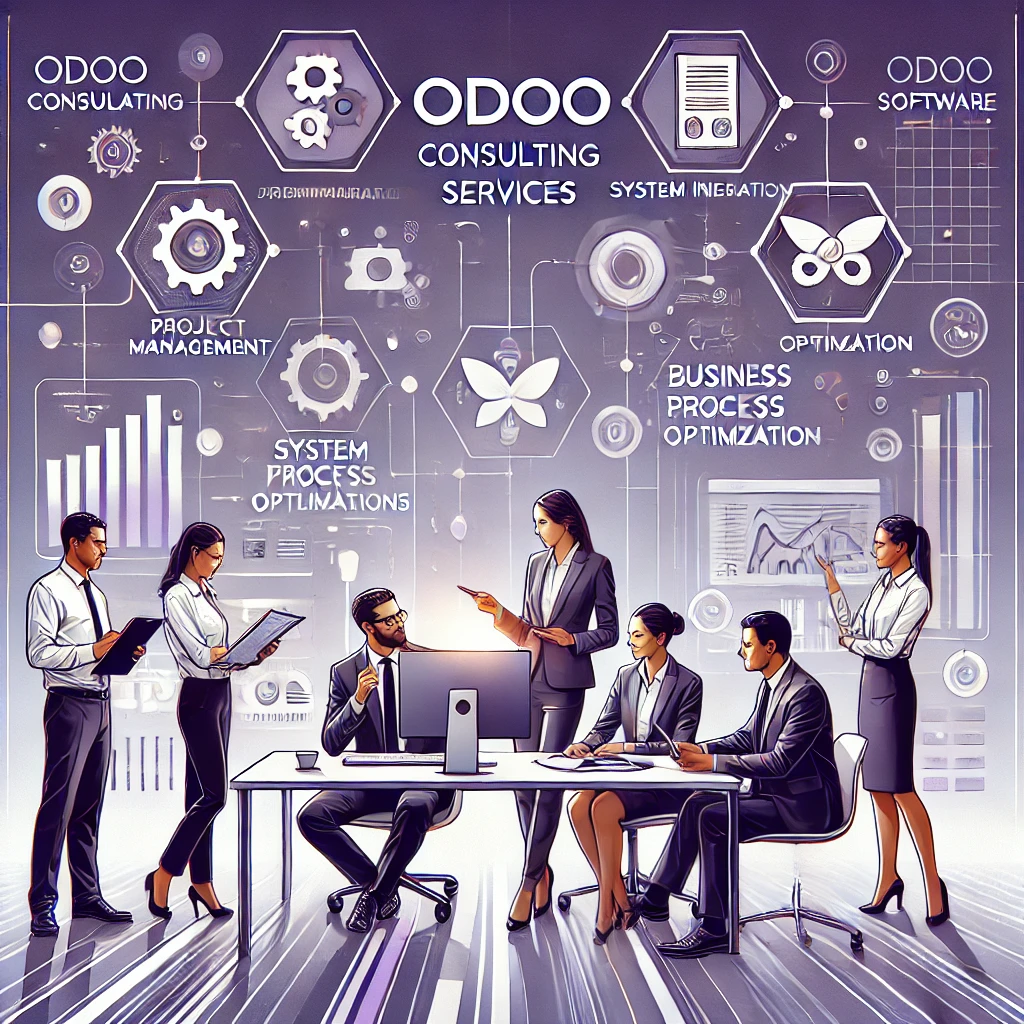
Why Spare Parts Inventory Matters in Manufacturing
A reliable inventory management system for spare parts is not just a support function, it’s a critical component of operational resilience. Unplanned downtime can cost manufacturers dearly, as stalled production affects revenue and disrupts entire supply chains. By maintaining an organized, strategically managed inventory of spare parts, manufacturing companies can reap multiple benefits:
- Reduced Downtime: Machines break unexpectedly, and production halts if a vital part is unavailable. Proactive inventory management minimizes these costly stoppages.
- Cost Efficiency: Keeping Inventory in excess is costly while understocking can lead to emergency purchases at premium prices. The right approach balances these costs.
- Enhanced Productivity: When essential parts are readily available, production teams can focus on maintaining quality and hitting productivity goals without disruptions.
With specialized expertise from a trusted Odoo development company, Odoo can be customized to adapt to these demands in manufacturing, ensuring companies can effectively manage their spare parts.
How Odoo Streamlines Spare Parts Inventory Management
Odoo’s integrated suite of applications offers manufacturers a holistic solution for spare parts inventory management. From real time tracking to the automation of critical processes, Odoo’s features address the unique challenges of managing Inventory in manufacturing environments.
Real Time Tracking for Enhanced Visibility
In a busy manufacturing plant, tracking the movement of spare parts manually can be difficult. Odoo simplifies this with real time tracking tools that offer total visibility into every component. This transparency enables manufacturers to monitor their stock across multiple warehouses and easily manage Inventory.
With real time tracking in Odoo, manufacturers gain:
- Immediate Insight into Inventory Levels: Knowing exactly where each part is and in what quantity improves planning and minimizes errors. This enhanced visibility ensures that staff can locate critical parts quickly.
- Rapid Response to Demand: When a sudden need arises, managers can see stock availability in real time, helping them make faster, data driven decisions.
- Optimized Allocation of Resources: Real time tracking aids in managing Inventory across locations, allowing for efficient resource allocation and reducing waste.
An Odoo development agency can customize the platform to ensure that real time tracking fits the manufacturing facility’s specific layout and logistical needs, allowing manufacturers to control their spare parts completely.
Automating Reordering to Prevent Stockouts
Manually reordering spare parts is time consuming and can lead to stockouts significantly if demands fluctuate. Odoo’s automated reordering feature alleviates this challenge by monitoring stock levels and triggering orders when Inventory falls below a set threshold.
Automated reordering delivers:
- Reduced Risk of Stockouts or Excess Inventory: Odoo automatically reorders parts based on pre set rules, preventing stock shortages and overstocking and saving on storage costs.
- Supplier Coordination: Through Odoo’s supplier integration, purchase orders are automatically sent when reorder levels are reached, minimizing lead times and ensuring parts arrive on schedule.
- Focus on High Impact Tasks: Automation frees up time that would otherwise be spent on manual inventory checks, allowing staff to focus on more strategic activities.
A top Odoo development company can precisely help configure these reorder points, considering each part’s usage rate and criticality. This ensures that Odoo’s automated reordering functions seamlessly within the manufacturer’s specific inventory workflow.
Stock Level Optimization for Leaner Inventory
One of the most significant challenges in manufacturing is maintaining a lean inventory while ensuring part availability. Odoo’s stock level optimization tools help manufacturing businesses retain the right amount of Inventory, reducing excess stock while avoiding costly emergency orders.
Odoo achieves stock optimization through the following:
- Data Driven Stocking Decisions: Odoo recommends optimal stock levels based on historical usage patterns, demand forecasts, and lead times, allowing businesses to avoid excess Inventory while ensuring availability.
- Categorization of Parts by Criticality: With Odoo, manufacturers can categorize spare parts based on their importance, frequency of use, and lead time, so stock levels are customized for each category.
- Lowered Carrying Costs: Optimizing stock levels prevents the financial drain of excess Inventory, freeing up capital for other business needs.
Manufacturing companies can partner with an Odoo development consultancy to maximize the benefits of stock level optimization. Such a consultancy can ensure Odoo is configured for optimal stock management, balancing operational readiness with cost efficiency.
Downtime Reduction through Preventive Maintenance
Unplanned equipment downtime is one of the most expensive problems in manufacturing, and Odoo’s Maintenance module is designed to help avoid it. This module, integrated with Inventory, enables preventive and predictive maintenance that minimizes the chance of unexpected breakdowns.
With Odoo’s Maintenance module, manufacturers can:
- Schedule Preventive Maintenance Proactively: By tracking equipment usage and performance, Odoo assists manufacturers in planning maintenance before issues arise, reducing downtime.
- Ensure Critical Parts Are Readily Available: By linking Inventory and maintenance, Odoo prioritizes critical spare parts so maintenance can be completed quickly without delays.
- Support Production Efficiency: The Maintenance module seamlessly integrates with Odoo’s production tools, offering insights into equipment health and usage, which aids in anticipating part requirements and avoiding downtime.
Engaging with an Odoo ERP development company to customize this integration ensures that maintenance schedules and inventory requirements are aligned, keeping production running smoothly and minimizing costly delays.
Additional Features That Enhance Spare Parts Inventory Management in Odoo
Odoo offers additional features that add further value to spare parts management, making the system more functional, user friendly, and versatile.
Multi Warehouse Management for Streamlined Operations
Manufacturing often involves multiple facilities or warehouses, making visibility across locations critical. Odoo’s multi warehouse management capability offers a centralized view of all Inventory, allowing manufacturers to transfer parts between warehouses as needed and reducing the risk of stockouts in high demand areas.
Advantages of Odoo’s multi warehouse management include:
- Consolidated Inventory Tracking: A centralized view of all stock ensures managers have visibility into every warehouse, simplifying decision making.
- Efficient Stock Allocation: By managing Inventory across locations, Odoo allows for the redistribution of parts based on demand, ensuring that critical parts are always in the right place.
- Simplified Logistics: Odoo’s integration with warehouse routing and shipping modules makes it easier to transfer parts between facilities.
Partnering with an Odoo POS development company can help manufacturers leverage multi location management, enabling effective and streamlined warehouse management.
Barcode and RFID Integration for Faster Tracking
Manual inventory tracking can slow operations and lead to errors. Odoo’s integration with barcode and RFID scanning tools makes data entry seamless, speeding up stock checks and improving accuracy.
Barcode and RFID integration offers:
- Accelerated Inventory Management: Scanning parts saves time compared to manual entry, allowing for quicker processing of stock movements.
- Higher Data Accuracy: Scanning ensures up to date, accurate inventory records by automating data entry.
- Simplified Audits: Barcode and RFID integration make inventory audits more manageable, enhancing compliance and record keeping.
An Odoo module development company with expertise in inventory optimization can implement this technology, making spare parts tracking more accurate and efficient.
Comprehensive Reporting and Analytics for Better Decision Making
Odoo’s analytics tools give manufacturers insights into key metrics like inventory turnover, carrying costs, and supplier lead times. These insights empower decision makers to manage Inventory proactively, based on data rather than guesswork.
With Odoo’s reporting and analytics, manufacturers can:
- Forecast Demand More Accurately: Analyzing usage patterns and trends allows for better demand planning, reducing the chance of stockouts.
- Identify Cost Savings: By monitoring carrying costs and stock levels, companies can identify areas to cut expenses and improve efficiency.
- Evaluate Supplier Performance: Analytics allow manufacturers to assess supplier reliability, ensuring they work with partners who consistently meet their needs.
For a tailored reporting experience, businesses can hire Odoo developers who understand the nuances of manufacturing and can configure Odoo’s analytics to deliver actionable insights.
Tailored Odoo Development Solutions for Seasonal Demand
Tailored solutions for your business needs.
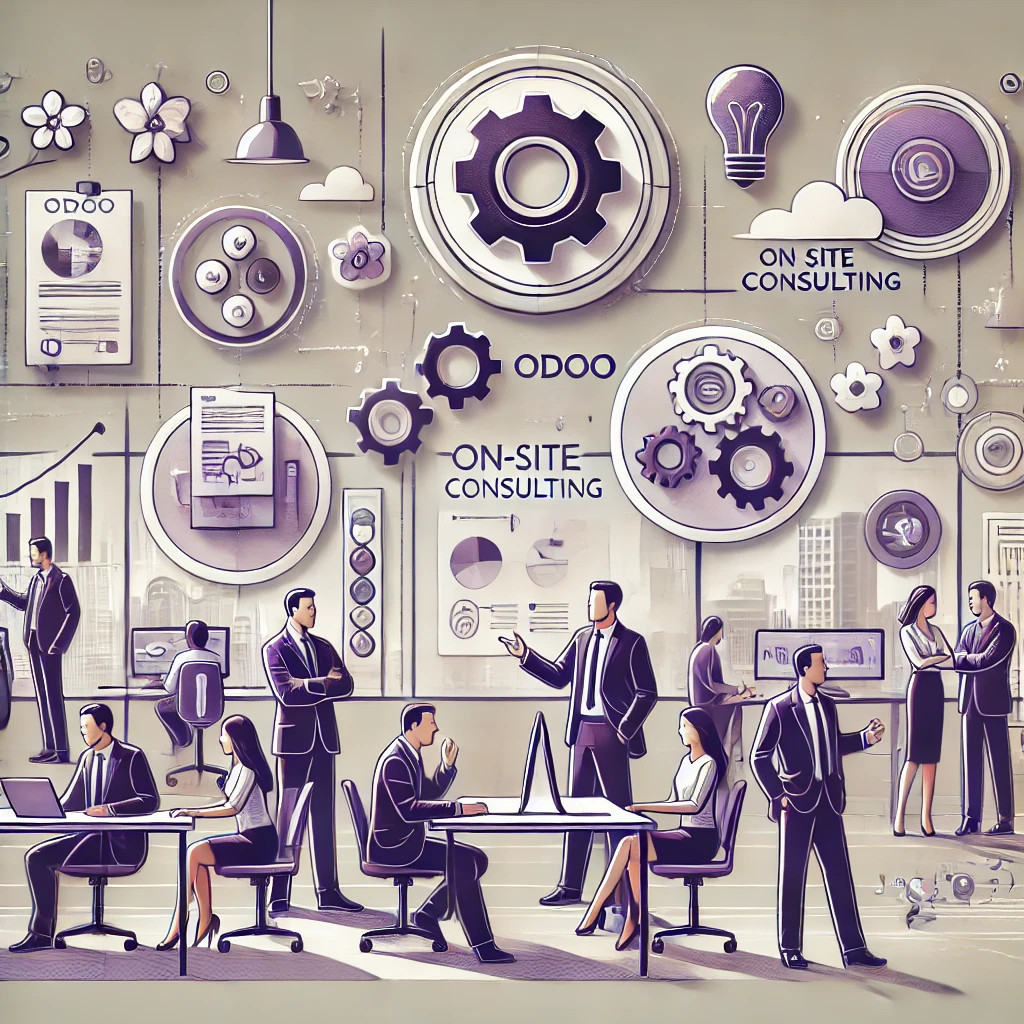
Real World Impact: Key Benefits of Odoo in Spare Parts Management
Manufacturing companies implementing Odoo for spare parts management often see tangible improvements in efficiency and profitability.
- Cost Savings: Optimizing stock levels and reducing manual tasks lead to lower Inventory and labour costs.
- Enhanced Productivity: Automation and real time tracking allow employees to focus on high impact tasks, improving overall productivity.
- Scalability and Flexibility: Odoo’s modular design allows it to grow alongside the business, adapting to the evolving needs of manufacturers.
Best Practices for Implementing Odoo in Spare Parts Management
For a successful Odoo implementation, manufacturers should consider these steps:
- Assess Inventory Requirements: Identify critical parts, their ideal stock levels, and reorder thresholds.
- Customize Odoo Modules: Work with an experienced Odoo development firm to set up Inventory, Maintenance, and Purchasing modules to align with business needs.
- Define Reordering Rules: Establish reorder points for each part, especially critical ones, to ensure availability.
- Train Employees: Ensure all users are trained on Odoo’s features, including tracking, ordering, and reporting.
- Monitor and Optimize: Regularly analyze performance data to refine inventory strategies and enhance efficiency.
Conclusion
Odoo is an adaptable, powerful ERP platform that addresses the challenges of spare parts inventory management in manufacturing. From real time tracking to automated reordering, downtime reduction, and comprehensive analytics, Odoo’s functionalities make it an invaluable tool for manufacturers aiming to maintain lean, efficient inventories. Partnering with a reputable Odoo development company ensures the system is configured for optimal performance, helping manufacturers streamline operations, reduce costs, and keep production lines running smoothly.
Hire Skilled Odoo Developers for Seasonal Efficiency
Tailored solutions for your business needs.
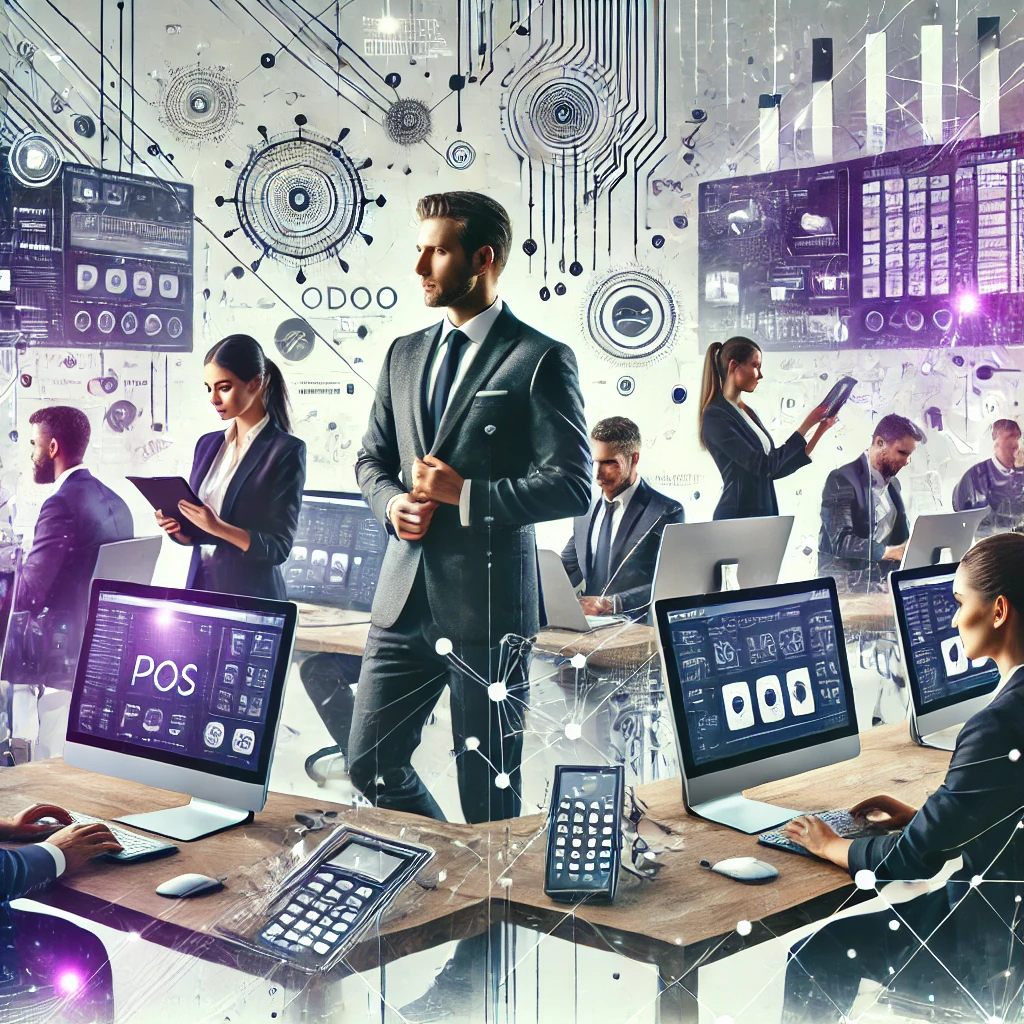
How SDLC CORP Helps Manufacturers Optimize Spare Parts Inventory Management with Odoo
For manufacturers looking to implement Odoo for spare parts inventory management, partnering with an expert Odoo development company like SDLC CORP can be transformative. With deep experience across the Odoo development industry, SDLC CORP offers comprehensive Odoo development services tailored specifically for manufacturing needs, guiding companies through every step of the Odoo development process from initial planning and customization to full implementation and post launch support.
SDLC CORP operates as a full spectrum Odoo development consultancy, bringing expertise to complex projects requiring a nuanced understanding of manufacturing operations and Odoo’s extensive capabilities. With our support, manufacturers can harness Odoo’s real time tracking, automated reordering, and maintenance integration to optimize their spare parts inventory. As a top Odoo development agency, our role is to ensure that each system configuration aligns with your production workflows, enhancing operational efficiency and cost effectiveness.
Our team at SDLC CORP includes certified professionals skilled in Odoo ERP development and specialized areas such as Odoo POS development and Odoo module development. This allows us to provide industry specific solutions that address unique challenges in inventory and maintenance management. For companies needing advanced customization, we can modify Odoo modules to fit your exact requirements, ensuring that every part of your spare parts inventory management is optimized and ready to support seamless production.
Whether you need a scalable solution for multi warehouse management or want to integrate barcode and RFID technology for efficient tracking, SDLC CORP is here to help. Our dedicated Odoo development firms provide end to end support and expertise, offering a level of customization that only top Odoo development companies can deliver. Suppose you’re looking to hire Odoo developers who understand the intricacies of manufacturing and inventory management. In that case, SDLC CORP has the knowledge and experience to bring your Odoo system to its full potential.