Introduction
Empty locations in Odoo’s Inventory module represent storage areas without products. Managing these effectively ensures better warehouse organization and accuracy in inventory operations. Below are the steps to manage empty locations in Odoo 18:
Steps to Manage Empty Locations in Odoo 18 Inventory
1. Enable Storage Locations
- Go to Inventory Configuration:
- Navigate to Inventory > Configuration > Settings.
- Enable Locations:
- Under the Warehouse section, enable Storage Locations.
- Click Save.
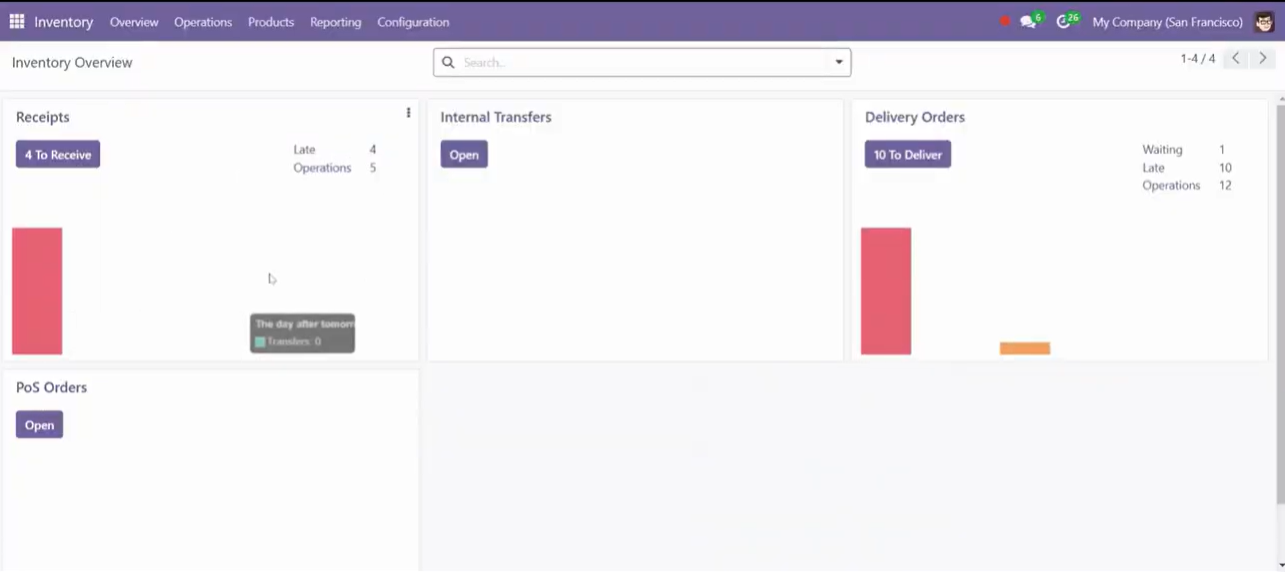
2. View Existing Locations
- Access Locations:
- Go to Inventory > Configuration > Locations.
- Check Location Details:
- Open each location to view its current stock and settings.
3. Identify Empty Locations
- Run an Inventory Report:
- Navigate to Inventory > Reporting > Inventory Valuation.
- Filter the report by Location and check for locations with a stock quantity of zero.
- Check Location Contents:
- Use the Inventory Overview dashboard to review stock at various locations.
- Empty locations will show no products or a stock quantity of zero.
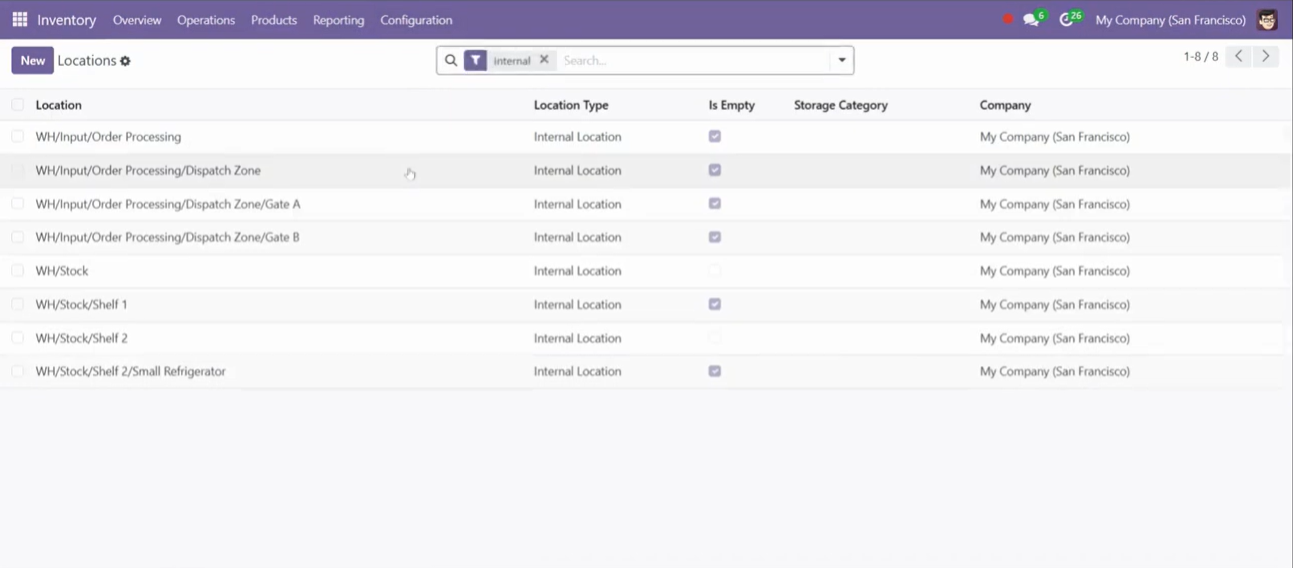
4. Reallocate Empty Locations
- Use Empty Locations for New Products:
- Assign empty locations for incoming stock by setting the default putaway rules or manually selecting the location during stock receipts.
- Update Putaway Rules:
- Go to Inventory > Configuration > Putaway Rules.
- Define rules to direct specific products to empty locations.
5. Perform Inventory Adjustments
- Create an Inventory Adjustment:
- Navigate to Inventory > Operations > Inventory Adjustments.
- Click Create and select the empty location to confirm its stock level.
- Verify Stock Levels:
- Ensure that the stock quantity is correctly recorded as zero for the empty location
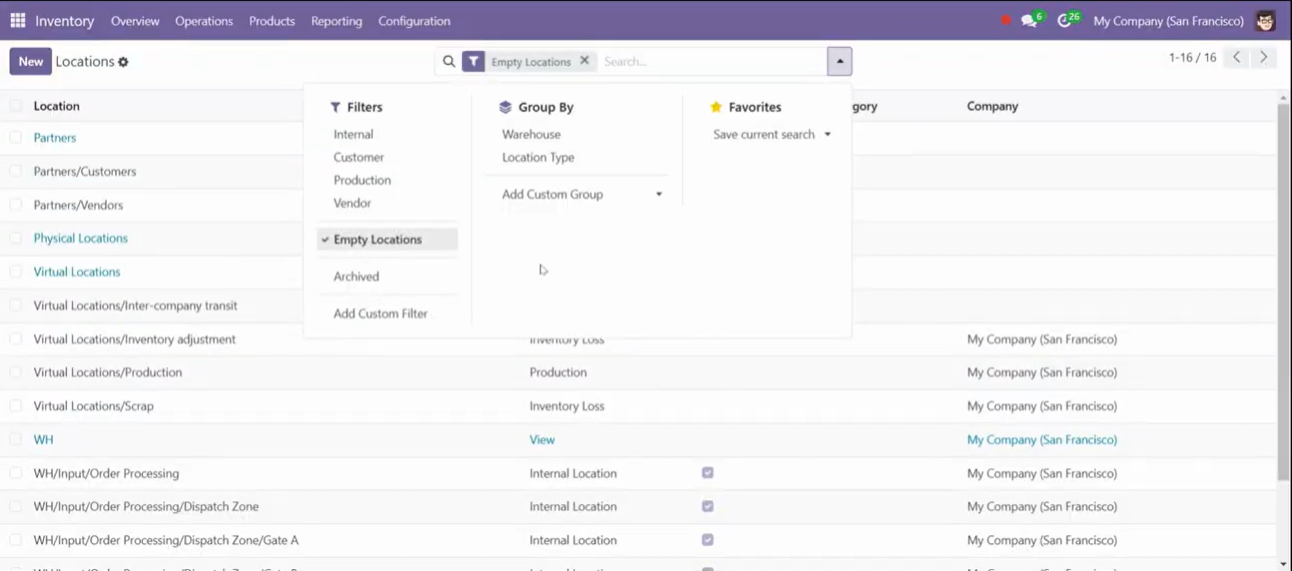
6. Archive Unused Locations (Optional)
- Identify Unused Locations:
- Locate storage areas that are empty and not actively used for operations.
- Archive Locations:
- Open the location record in Inventory > Configuration > Locations.
- Mark it as Archived to hide it from operational screens while keeping it available for future use.
7. Monitor Empty Locations Regularly
- Set Alerts for Empty Locations:
- Configure rules or filters in reports to flag locations that become empty.
- Review Periodically:
- Periodically check the Inventory dashboard to identify and reallocate empty locations.
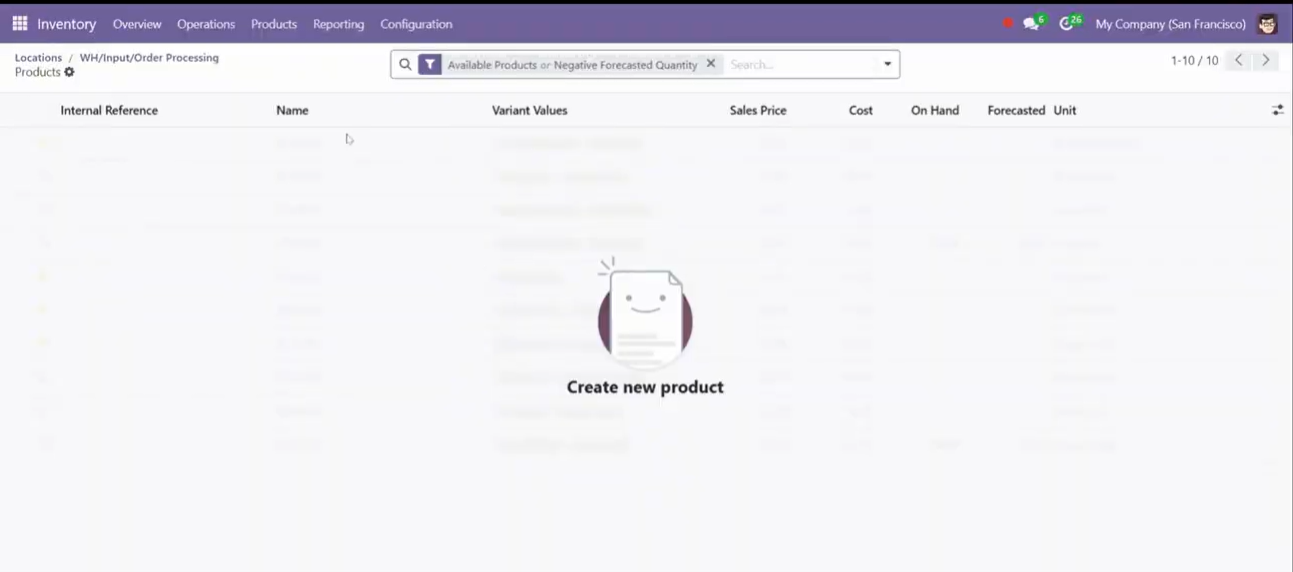
8. Optional: Automate Empty Location Management
- Use Automated Rules:
- Configure reordering or putaway rules to dynamically allocate stock to empty locations.
- Integrate with Barcode Scanning:
- Use barcodes to streamline the process of identifying and updating empty locations during stock moves.
Conclusion
Managing empty locations in Odoo 18 ensures efficient warehouse operations and better space utilization. By regularly monitoring and reallocating these locations, you can maintain an organized inventory system and optimize your storage capacity.
Expert Odoo ERP Solutions Tailored
Streamline Operations and Boost Growth with Odoo ERP Solutions
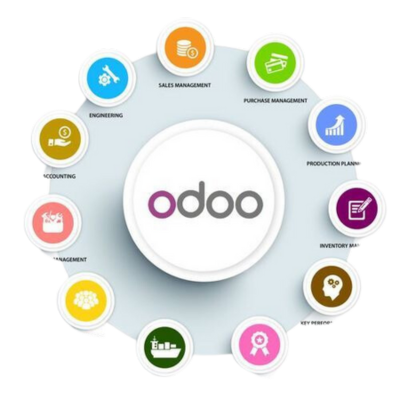
How SDLC CORP Can help to manage empty locations in odoo 18 Inventory ?
SDLC Corp offers expert Odoo development services to help businesses optimize their operations with tailored solutions. As one of the top Odoo development companies, they specialize in Odoo custom development, Odoo application development, and Odoo ecommerce development, providing scalable, integrated solutions to meet specific business needs. Whether you want to hire Odoo developers or hire Odoo experts, SDLC Corp ensures seamless implementation and support, helping businesses fully leverage Odoo for growth and efficiency.