Introduction
RPA and Quality Assurance: Over the last five years, the emergence of new technology and procedures has sparked a transformation in quality assurance(QA). With the demand for faster deployments and shorter time-to-market, organizations must implement an agile and automated QA and testing strategy that guarantees timely releases without sacrificing quality.
Organizations are increasingly adopting robotic process automation (RPA) as an essential part of digital transformation because it is simple to implement and uses software bots to reduce operational costs while improving efficiency and accuracy.
Thus, RPA is ushering in a new age of enterprise automation powered by artificial intelligence (AI) and machine learning (ML), and quality assurance is a critical automation candidate.
How Can An Organization Evaluate RPA Implementation?
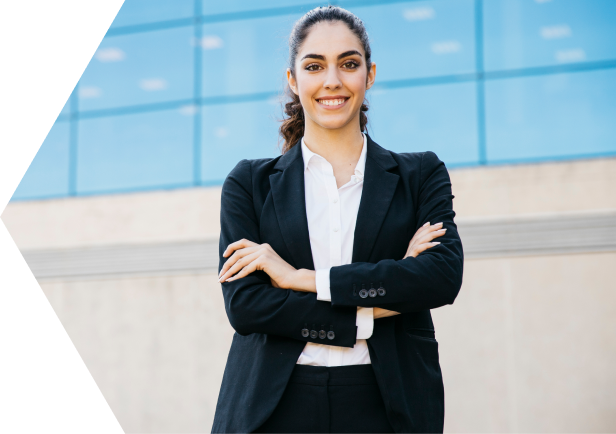
The Best Approach for Enabling RPA in QA
End-to-end testing and QA offerings for the organization must include a comprehensive RPA implementation plan, as shown below:
Step 1:
Identify repetitive QA team duties that can be optimized by implementing RPA.
Step 2:
Determine whether each procedure requires manual or automated testing.
Step 3:
Rather than testing the complete process, only the applications/actions/outputs are impacted or generated by the RPA bot.
Step 4:
You can enable end-to-end automation scripting by combining different open-source test automation tools.
Step 5:
Create a single automation script that handles everything from creating test data to bot execution and validation across all affected applications/systems.
Step 6:
Reuse the automation script in more advanced settings, such as system integration testing (SIT) and user acceptance testing (UAT).
The Advantages of Using RPA in Quality Assurance Processes
Level Up Quality: RPA for Enhanced QA!
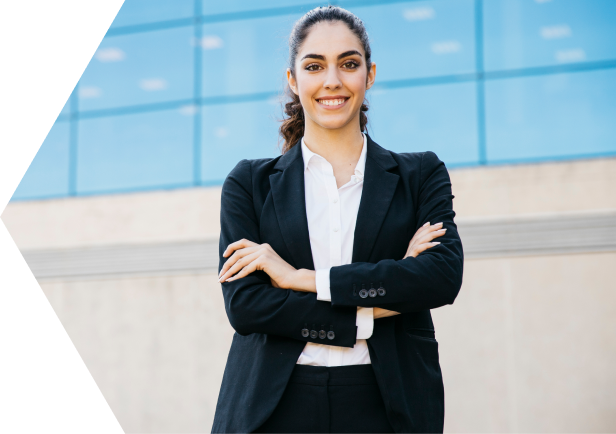
Explore our other insights!

Understanding RPA and its Various Industry Applications
Introduction RPA Industry Applications: Robotic Process Automation (RPA) is an innovative technology that automates mundane, repetitive tasks and
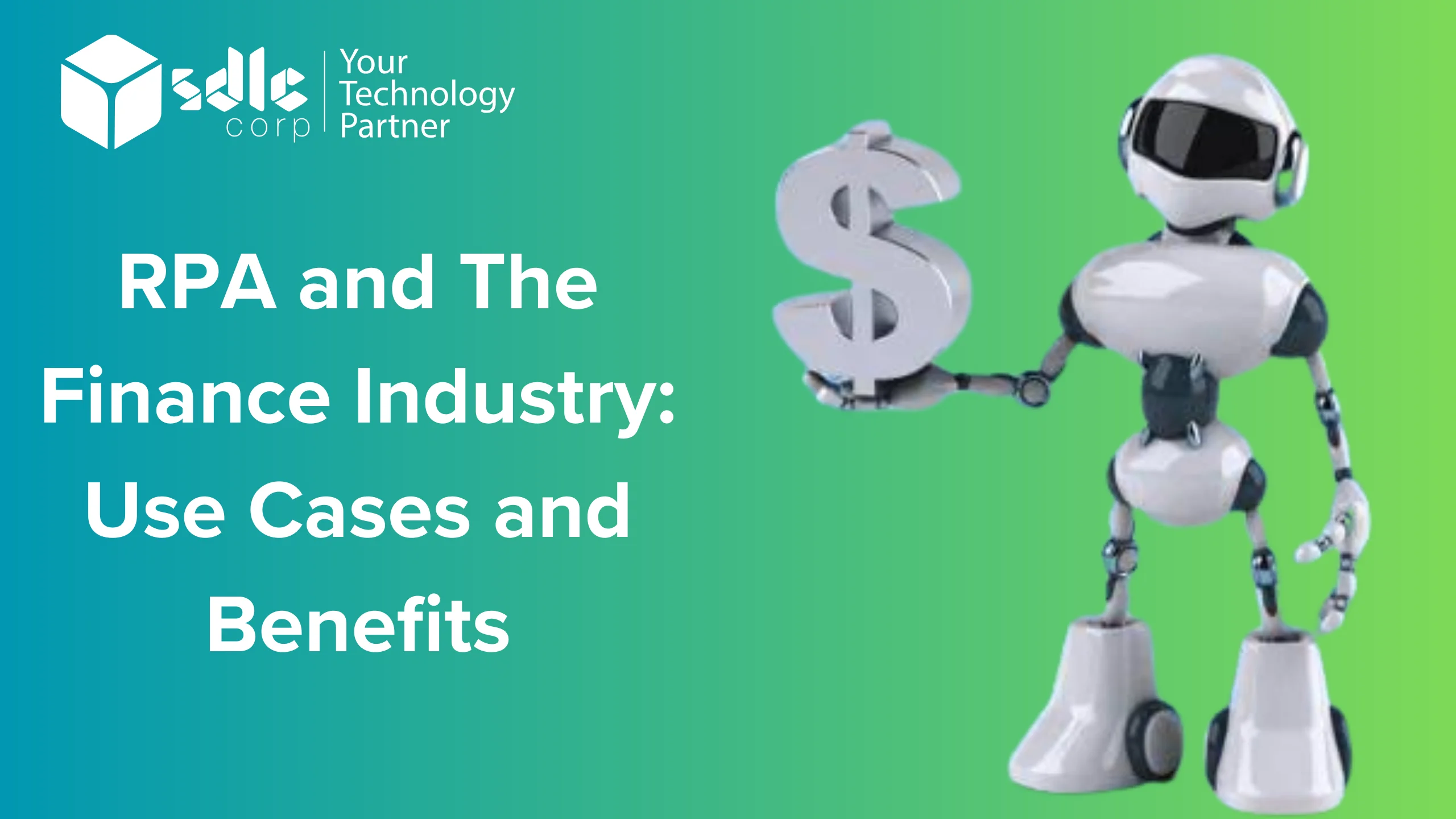
RPA and The Finance Industry: Use Cases and Benefits
Introduction RPA and The Finance Industry: Robotic Process Automation (RPA) is a rapidly growing technology transforming various industries
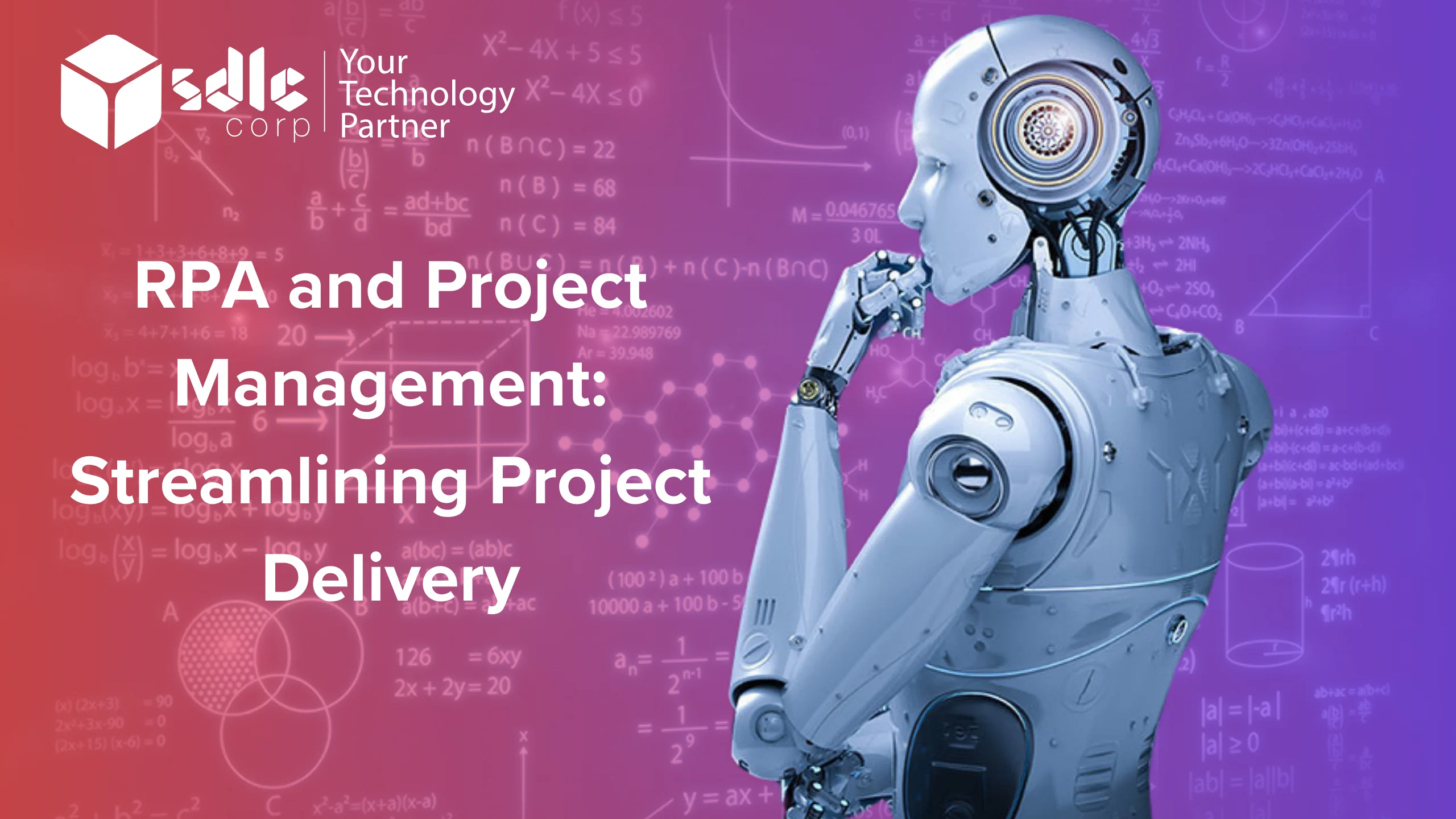
RPA and Project Management: Streamlining Project Delivery
Introduction RPA and Project Management: In today’s fast-paced business world, companies always look for new ways to increase
Here Are Some Statistics and Analytics Related to the Impact of RPA on Product Quality
1. According to a survey by Deloitte, 53% of organizations that have implemented RPA have seen an improvement in the quality of their products and services.
2. A study by McKinsey & Company found that organizations that have implemented RPA have seen a 30% improvement in quality and accuracy and a 25-50% reduction in processing time.
3. In a case study published by Automation Anywhere, a global manufacturing company reduced product defects by 60% after implementing RPA in its quality assurance processes.
4. The global RPA market is anticipated to reach $25.56 billion by 2027, with a compound annual growth rate (CAGR) of 33.6% from 2020 to 2027, according to a study by Grand View Research. This growth is partly driven by the increasing adoption of RPA for quality assurance and other automation use cases.
5. Another report by Forrester Research found that organizations that have implemented RPA have seen a 4x improvement in customer satisfaction and a 40% reduction in customer complaints, which can be attributed partly to improved product quality and consistency.
Overall, these statistics and analytics suggest that RPA can effectively improve product quality and reduce errors in quality assurance processes. As the market for RPA continues to grow, more organizations will likely turn to this technology to increase efficiency and consistency in their quality assurance efforts.
Benefits of RPA in Improving Product Quality and Competitiveness
Similarly, RPA can be used to automate the collection and analysis of data related to product quality. By automating data collection and analysis, companies can quickly identify trends and patterns that may indicate quality issues, allowing them to take corrective action before problems become widespread.
In addition to improving product quality, RPA can help companies improve their overall competitiveness. By automating routine tasks, employees can focus on more strategic tasks that add value to the organization. This can help companies innovate faster, respond more quickly to market changes, and ultimately gain a competitive advantage.
The Bottom Line
RPA has the potential to significantly improve product quality by automating routine tasks and improving accuracy and consistency. As a result, companies incorporating RPA into their quality assurance processes can expect significant benefits, including improved efficiency, reduced costs, and increased competitiveness.
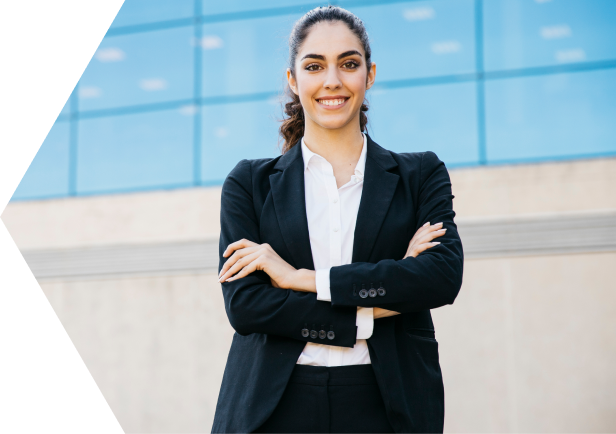
FAQs
1. How can RPA help improve product quality?
RPA can lower the risk of human error, which is a significant contributor to product defects, by automating routine tasks. Additionally, RPA can help to enforce standard operating procedures (SOPs), ensuring that all jobs are performed consistently and according to best practices.
2. How can RPA be used for quality assurance?
RPA can be used in several ways to improve quality assurance, including automating data entry and analysis, monitoring and analyzing product performance data, and performing automated testing of products and software.
3. What are the benefits of using RPA for quality assurance?
The benefits of using RPA for quality assurance include increased accuracy and consistency in data entry and analysis, faster and more efficient testing, and improved compliance with regulations and standards.
4. Can RPA replace human workers in quality assurance?
RPA is not meant to replace human employees; it is intended to enhance their abilities by automating repetitive tasks and freeing up time for more involved and valuable activities.
5. What industries can benefit from using RPA for quality assurance?
Virtually any industry that relies on consistent and accurate data analysis and testing can benefit from using RPA for quality assurance, including manufacturing, healthcare, finance, and technology.
6. What are some examples of RPA in quality assurance?
Examples of RPA in quality assurance include automating data entry and analysis for product performance testing, automating testing of software applications, and monitoring and analyzing customer feedback data to identify product defects.