Introduction
The Internet of Things (IoT) has transformed many manufacturing industries. An interconnected system of gadgets called the Internet of Things (IoT) exchanges data with one another. For example, in manufacturing, IoT can be used to monitor and control production processes, as well as to optimize supply chains and improve product quality. In this blog, we will look at some of the IoT Applications and Benefits in manufacturing.
What is Industrial IoT (IIoT)?
Before building your own IIoT solution, you must understand industrial IoT and how it changes manufacturing operations.
“Industrial Internet of Things” refers to a class of linked devices, sensors, and equipment used in an industrial setting that may communicate with other devices or systems via an internet network.
Regarding industrial applications, the Internet of Things has served as a stepping stone and foundation for the next level of production automation.
Over time, technology developers have applied the fundamentals of IoT to the manufacturing industry, developing intelligent factories that use a high level of device interconnectivity to increase production efficiency and quality.
Applications of IoT in Manufacturing

1. Predictive Maintenance
Nothing has a more significant negative impact on a manufacturing business than machine downtime. According to experts, the average manufacturer sees 800 hours of equipment downtime annually, amounting to an industry-wide cost of $50 billion in unplanned expenses annually.
So what may be producing such severe problems that firms cannot operate? The solution is straightforward: a need for proper and anticipatory maintenance.
When maintenance in the industrial world is reactive rather than proactive, producers are left attempting to figure out what the problem is, how to fix it, and how much it will cost. These concerns are addressed by predictive maintenance provided by industrial IoT solutions.
2. Quality Control
IoT sensors can monitor product quality in real-time, allowing manufacturers to identify and address issues before they become widespread.
3. Inventory Management
IoT sensors can track inventory levels in real time, allowing manufacturers to optimize their supply chains and reduce inventory costs. (Read more about Blockchain in Supply Chain | Track and Trace with Blockchain Technology)
IoT in Manufacturing: Click to Boost Efficiency Now!
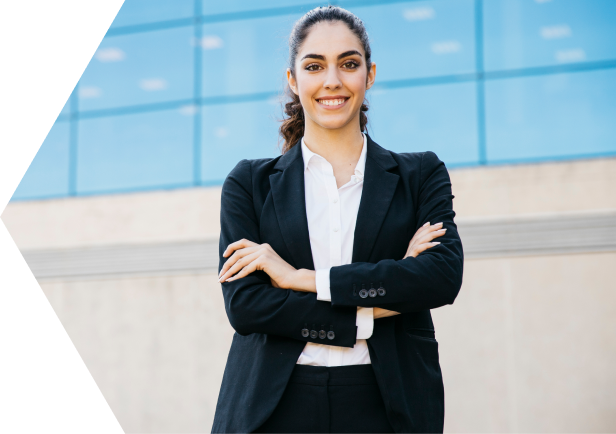
4. Energy Management
Energy utilization in industrial facilities can be monitored by IoT sensors, enabling producers to pinpoint locations where energy usage can be decreased.
5. Worker Safety
Benefits of IoT in Manufacturing
The increasingly complicated manufacturing scene necessitates even more capable automation systems to meet consumer objectives.
Manufacturing companies embracing the Industrial Internet of Things benefit on multiple levels, including production efficiency, customer happiness, and overall business decisions. The following are the most notable advantages of incorporating the Internet of Things into a manufacturing environment:

1. Automated Data Collection
In more traditional settings, employees collect data manually. Furthermore, paper-based gathering and storage methods frequently result in human errors and errors that compromise overall data integrity.
On the other hand, connecting equipment and gadgets to the internet enables automatic, real-time data collecting. This gives correct data for analysis, resulting in better business decisions.
2. Increased Productivity
Manufacturers with IoT-enabled manufacturing processes benefit from increased machine utilization. As previously stated, networked machines provide a constant supply of data that offers insights into equipment operation.
This lets manufacturers improve the general effectiveness of their machines and get the most out of them while they are in use.
Furthermore, using IIoT devices results in greater utilization of human capital. Smart gadgets can be used to do more mundane and repetitive chores, freeing up people for more critical jobs.
Explore our other insights!
3. Real-time Production Visibility
IoT allows firms to track production in real-time and gain comprehensive visibility into shop floor activities. Connecting to and drawing data from machines on the shop floor provides supervisors and managers with an understanding of what is happening across the production.
This data can be analyzed to provide valuable insights, helping managers to identify problems and their leading causes. As manufacturers enhance the system, this results in constant improvement.
IoT: Transform Manufacturing Now! Click for Benefits!
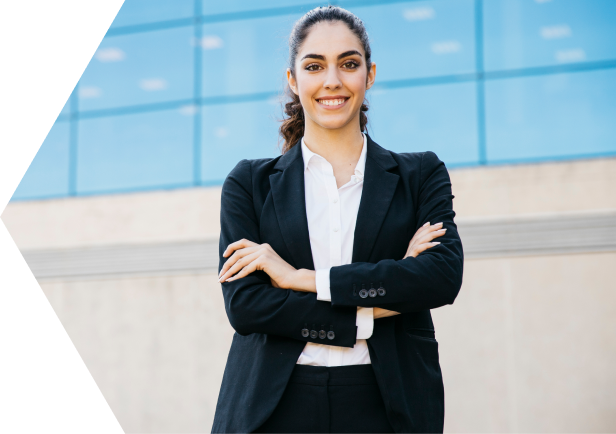
4. Reduce Quality Defects
Embracing IIoT forces manufacturers to automate production procedures. By removing the human element from the most automated systems, faults and mistakes that result in defective items leaving the production line are eliminated.
Because of enhanced customer satisfaction and brand recognition, the business becomes more profitable with much fewer quality flaws.
5. Lower Manufacturing Costs
Manufacturers use the Industrial Internet of Things to lower manufacturing costs and boost process efficiency.
Operators can improve their operations by utilizing linked devices, automating a significant percentage of the human input and data collecting involved with traditional processes.
Furthermore, machine monitoring capabilities provide data regarding equipment health, allowing manufacturers to implement preventive maintenance. This reduces expenses by reducing downtime and costly repairs.
Examples of IoT in Manufacturing
We’ve worked with a few manufacturing companies that have seen connected goods used successfully.
An intelligent fire truck provider should be able to provide standard innovative fleet management features, such as proactively flagging vehicles for essential service to save downtime. However, the trucks also had gadgets linked to the fire suppression and rescue equipment.
This allowed for predictive maintenance and made certain aspects of the firefighter’s job easier, such as regulating water pressure and controls. Positions on the vehicle that would typically require three firefighters could thus be handled by one, freeing up the workforce for fighting fires. That is a degree of added value that can potentially actively save lives.
Another example was a non-traditional transportation fuel source that was working towards implementing a touchless maintenance program. Extended downtime was becoming a concern, with approximately 550 uncrewed fueling stations and 150 technicians nationwide.
The corporation needed to put in place a system that allowed them to quickly connect with these unmanned systems to verify they were working correctly, to get from alarm to repair in a shorter amount of time, and even to uncover flaws before they caused the station to fail.
Working with SDLC Solutions to adopt their touchless technology allowed the company to maximize its staff, ensuring that problems could be resolved on the first call and contributing to higher efficiency and value.
IoT Solutions and SDLC Solutions

1. Create and Discover Value
We begin by utilizing our enterprise knowledge to assist you in developing and defining your IoT value. This goes beyond infrastructure considerations; it is a collaboration in understanding how to generate business reasons and models to create a value case for investing in IoT for all stakeholders and speeding its adoption.
2. Empower IoT Infrastructure Support
Our enterprise-class Empower data platform provides analytics as a Service to assist you in managing the orchestration and operations of your data analytics. Empower handles much of the heavy lifting of data collecting, mapping, modeling, and cataloging, giving you ultimate control over your information and maximizing the value of your IIoT infrastructure.
3. Concentrate on Action Results
We use our knowledge in enterprise asset management, enterprise machine learning, and AI solutions to assist you in developing action systems that will allow you to achieve desired results with your data.
We’ll collaborate with you to create designs such as predictive maintenance models, asset management, and connected field service to turn your IoT data into actionable solutions, ensuring you get the most out of your investment.
Please contact our team if you want to start deploying enterprise IoT solutions or learn more about SDLC for manufacturing.
Enterprise Mobile App Development Company
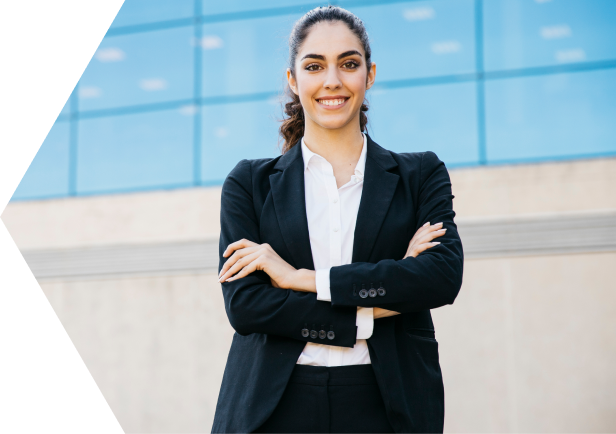
Conclusion
The Internet of Things has tremendous potential in manufacturing, offering a wide range of applications and benefits. By using IoT sensors to monitor and control production processes, optimize supply chains, and improve product quality, manufacturers can reduce costs, increase efficiency, and improve customer satisfaction. It will be fascinating to watch how IoT technology changes the manufacturing sector in the years to come as it continues to advance.
FAQs
1. What are some specific IoT applications in manufacturing?
Some specific IoT applications in manufacturing include real-time monitoring of production processes, asset tracking, predictive maintenance, and supply chain optimization.
2. How can IoT improve operational efficiency in manufacturing?
IoT can improve operational efficiency by enabling real-time monitoring and control of production processes, reducing the need for manual intervention, and enabling automated decision-making.
3. What is predictive maintenance, and how does IoT enable it?
Predictive maintenance uses data and analytics to predict when equipment will likely fail, enabling maintenance to be scheduled before a breakdown occurs. IoT enables predictive maintenance by collecting data from sensors on equipment and analyzing it to identify patterns and trends.
4. How can IoT improve product quality in manufacturing?
IoT can improve product quality by enabling real-time monitoring of production processes and identifying deviations from expected outcomes. This allows corrective action to be taken before defective products are produced.
5. How can IoT enable supply chain optimization in manufacturing?
IoT can enable supply chain optimization by providing real-time visibility into the location and status of inventory, enabling better planning and scheduling of production and logistics activities.